Where Are NOBL Rims Made
The short answer is China—because we found an employee-centric, innovative manufacturer—but the long answer is a far more interesting journey that includes our review of many factories in Taiwan and China.
It’s About Quality Control
Product performance and stability is better with strategic outsourcing of raw materials: Toray microfiber pre-cleaning cloth made in Japan, mold release agent from the United States, high density alloy molds, perforated bricks taken from the aviation industry, thinner and more flexible ducts produced in Taiwan, etc. This precision can even go beyond raw materials, and apply to the manufacturing process itself.
During research and development, the layup design of carbon fiber rims requires precision. Every adjustment to the layup requires an abundance of experimental testing, whereas in production, it demands more from manual operations and the composition of raw materials. A laboratory can test the products from the production line at any time to ensure stability.
To achieve our vision, we needed more than a foundry factory with a traditional manufacturing process. To possess the passion for new technologies and materials, to innovate beyond simple mass production would be instrumental to our longevity in this business. As a result, we set out to find the perfect factory to create a long term partnership with, no matter the location.
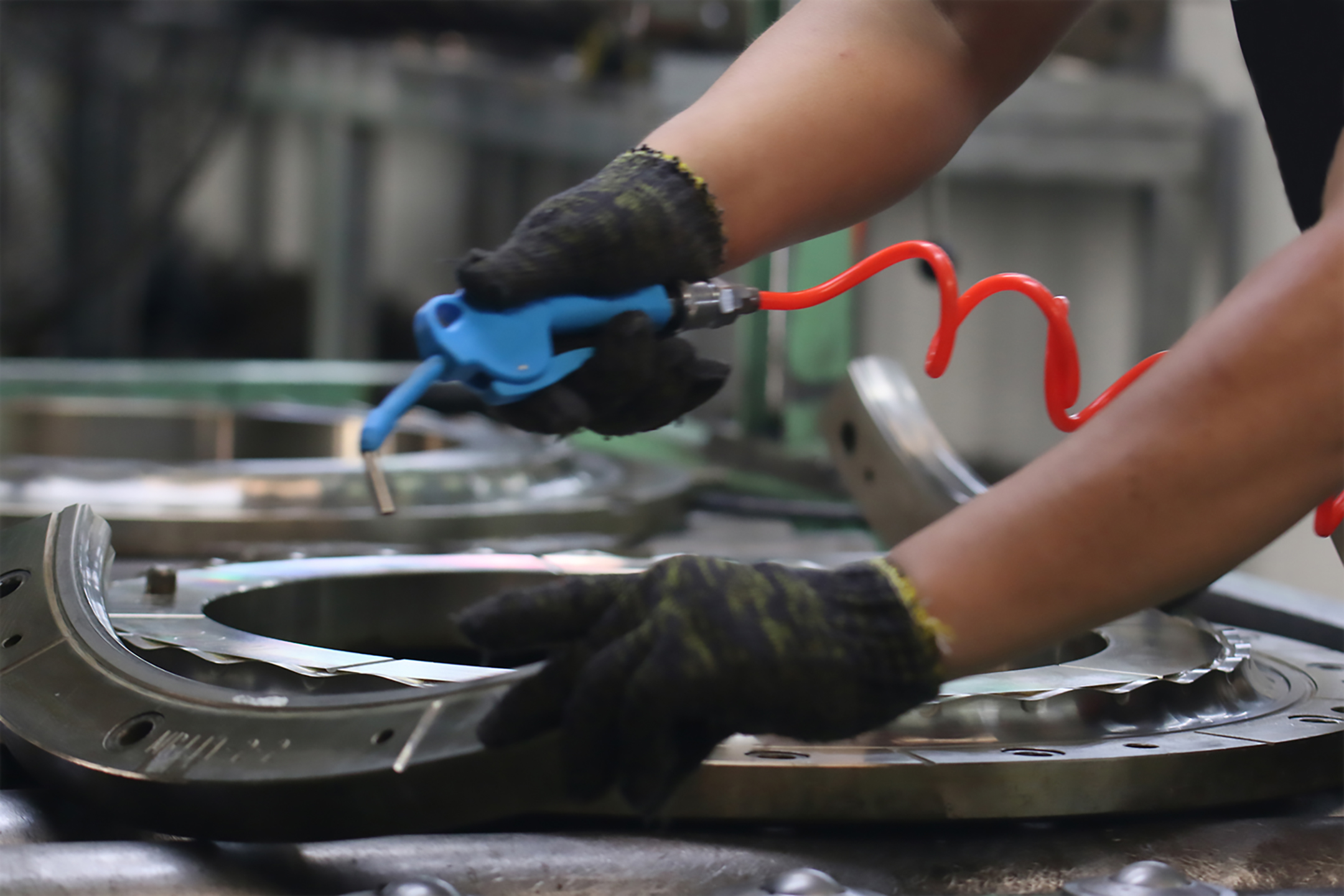
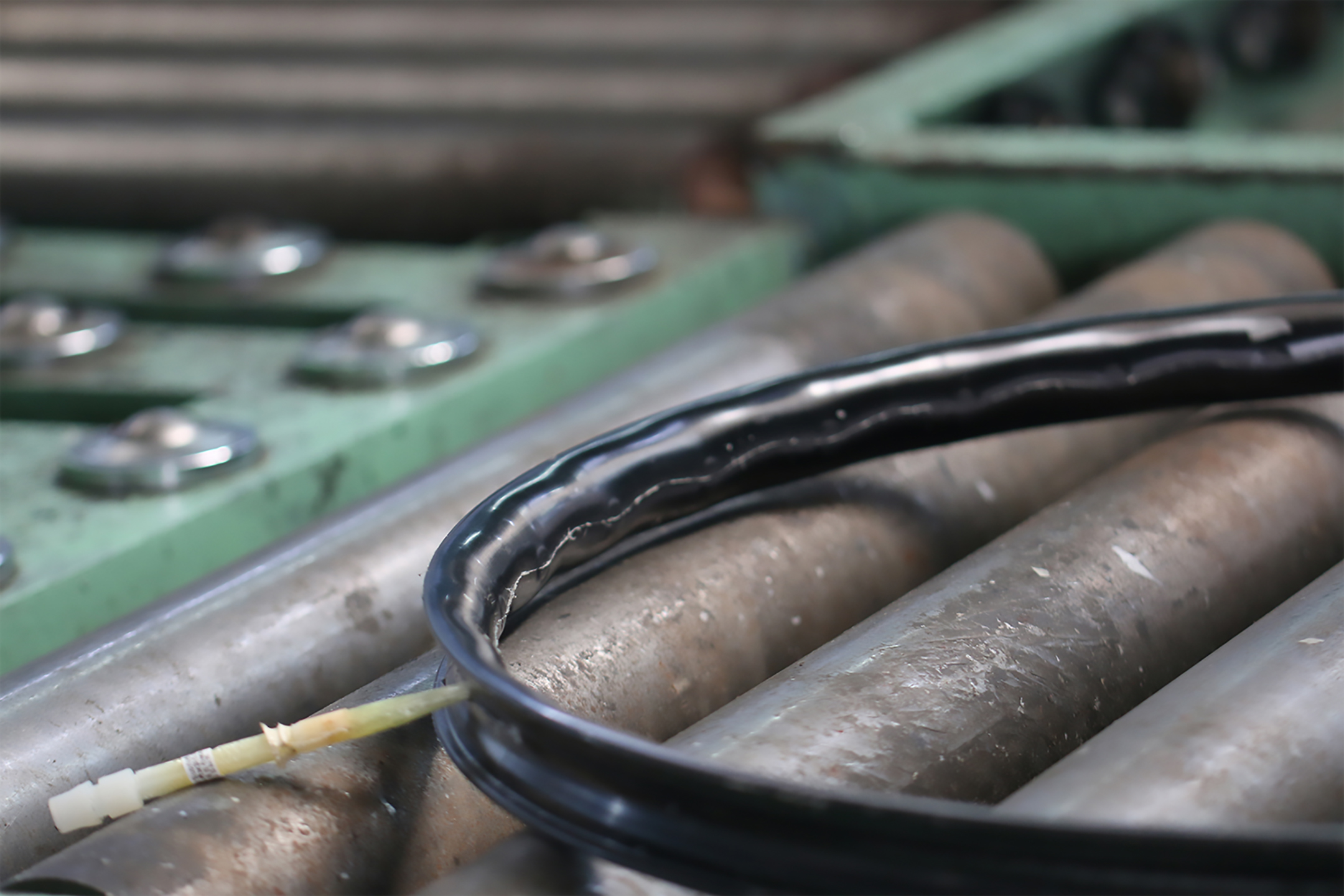
Exploring Factories
As you can imagine, it’s quite an investment to purchase a bunch of expensive molds in a foreign country. We found that China had been advancing in composite technology much more rapidly than Taiwanese companies. We visited a host of Taiwanese manufacturers, and to our surprise, there were a number of challenges that became large hurdles for us in doing business with them. Some were no more than distribution centers as their actual manufacturing was in mainland China (despite having “Made in Taiwan” stickers on their products). This caught us by surprise.
We also discovered that many of these Taiwanese factories often used temporary workers from nearby countries, as opposed to having a permanent Taiwanese workforce. Local employees were often more expensive, and sourcing workers from other countries was far cheaper. The high turnover of some of these employees made us nervous as we felt that it was essential to have experienced, long term workers creating our products. Having top notch consistency and quality control were of utmost importance to our product. Lastly, factories based in Taiwan tended to be massive, making it very difficult for a small company such as NOBL to have much influence in the design and engineering process.
For those reasons and others, we ended up deciding on a manufacturer in Xiamen, China. Xiamen is just off the coast of Taiwan – a short flight from Taipei. There are about 30 carbon rim factories in the city, making for an extremely competitive environment that lends itself to significant-tech advancements in short periods of time. It’s a vibrant coastal city and is known as one of the most desirable cities to live in China.
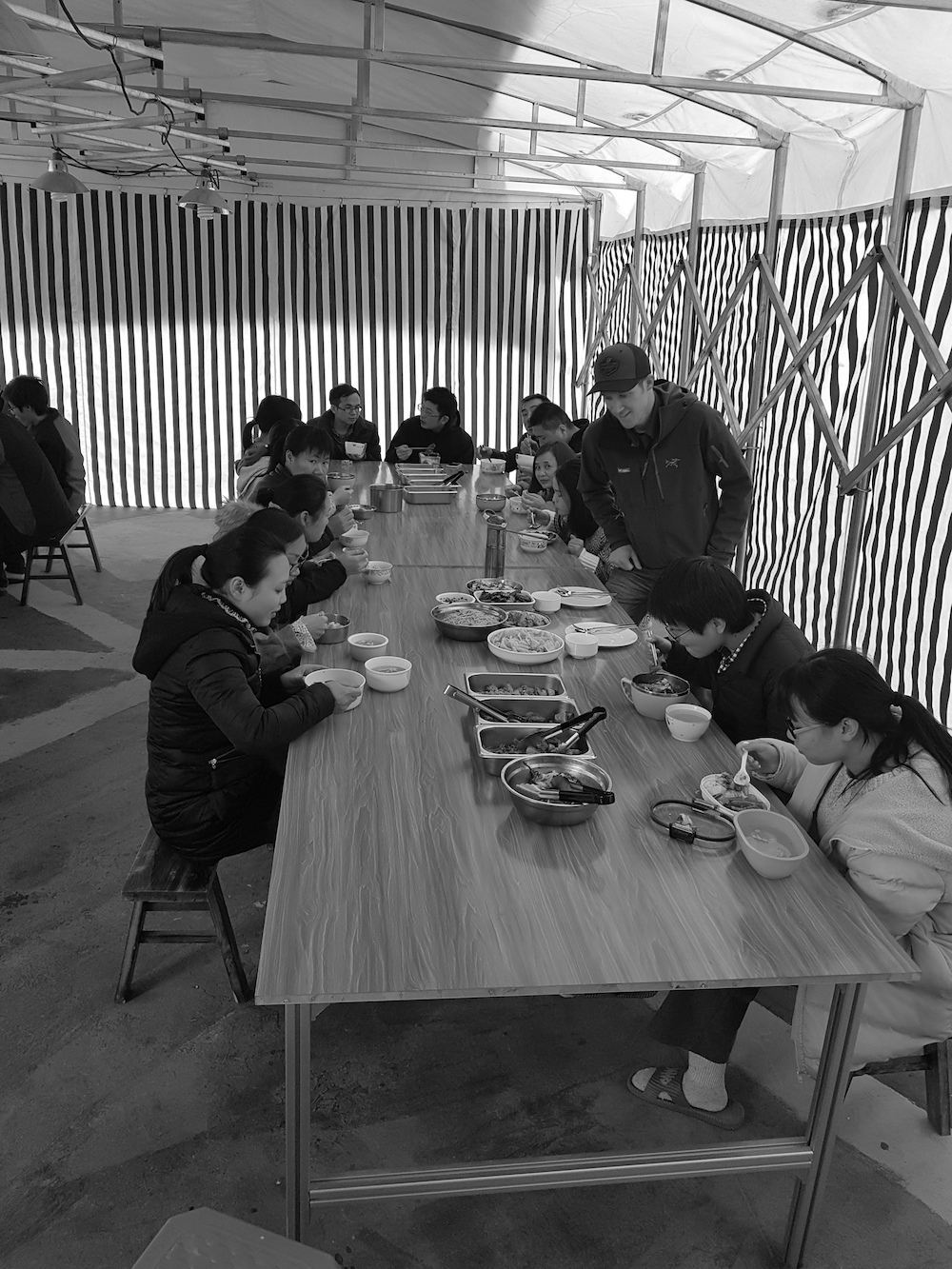
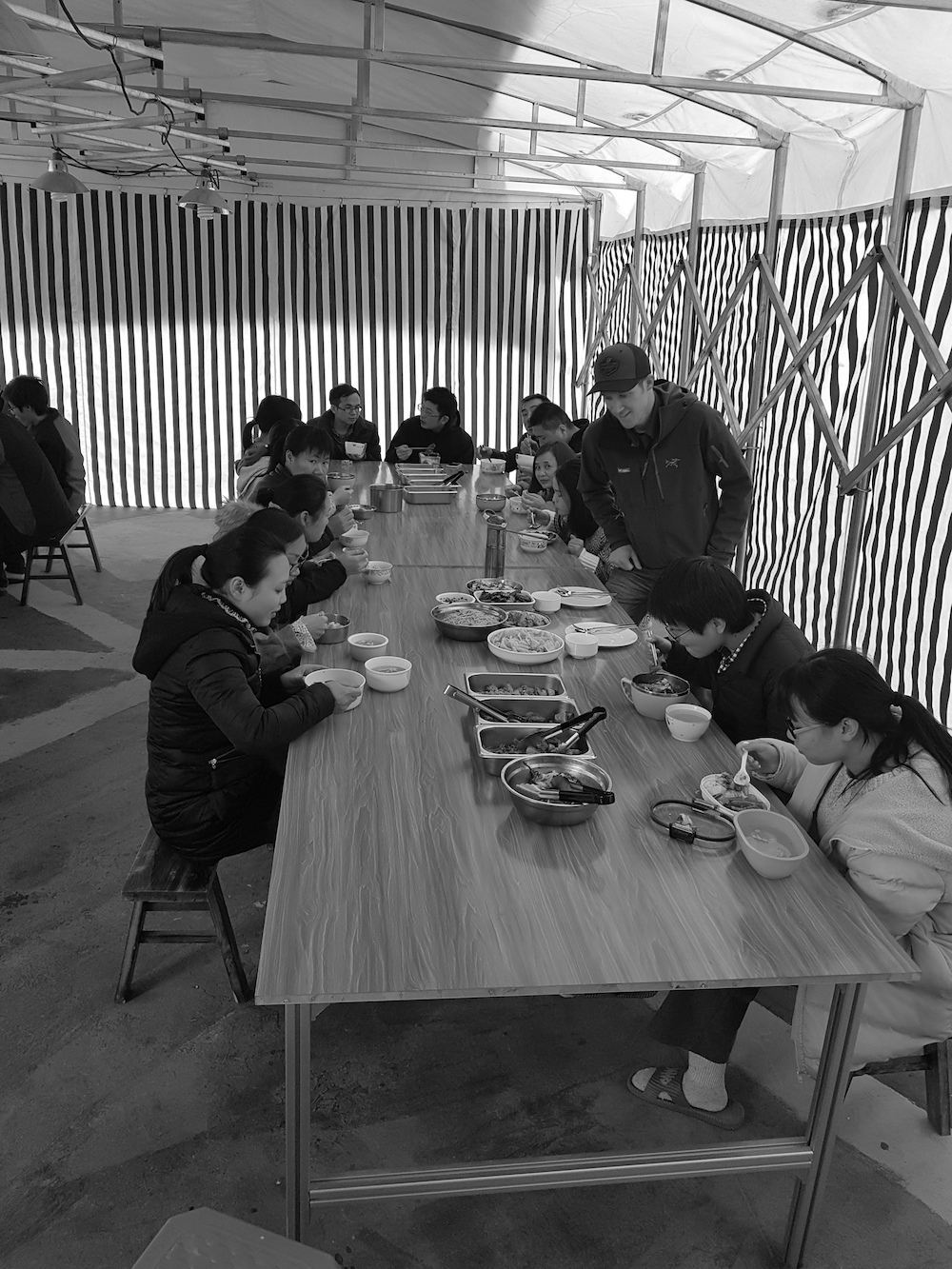
Overcoming Stereotypes
There is a stereotype that Chinese factories are all crowded, noisy and unhygienic operations. This couldn’t be further from the truth for the factory we work with. The floors are clean enough to eat off of, and a progressive work environment easily rivals that of the tech companies in the West. The break rooms feature an onsite chef who keeps the staff well fed with delicious meals. Some of the food is actually grown on the rooftop garden right onsite! After lunch everyone enjoys naptime (or just like our culture back home, you can go on your cellphone). Wait, naptime? Yes, you heard right, everyone has their own comfy cot and you get an hour to relax after lunch. If you don’t want to chill, there is a recreation room full of various board games and a ping pong table. Competition is fierce.
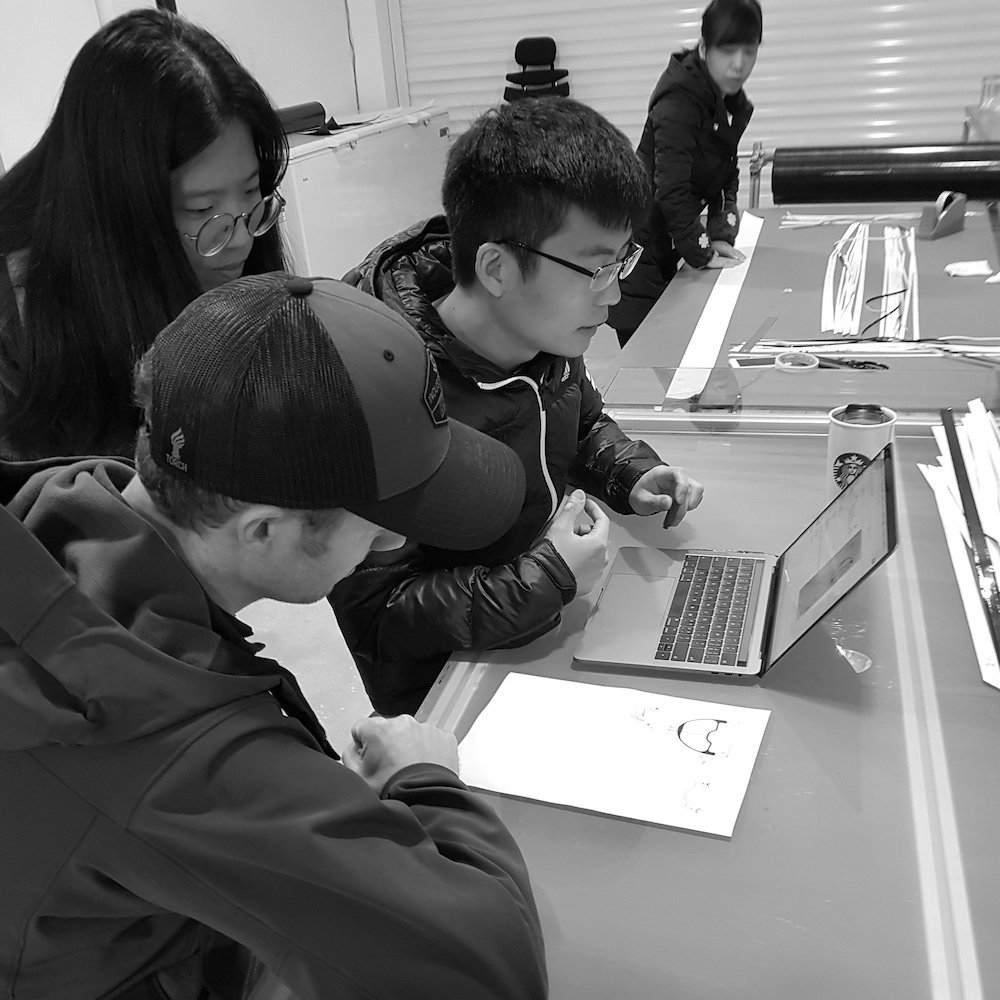
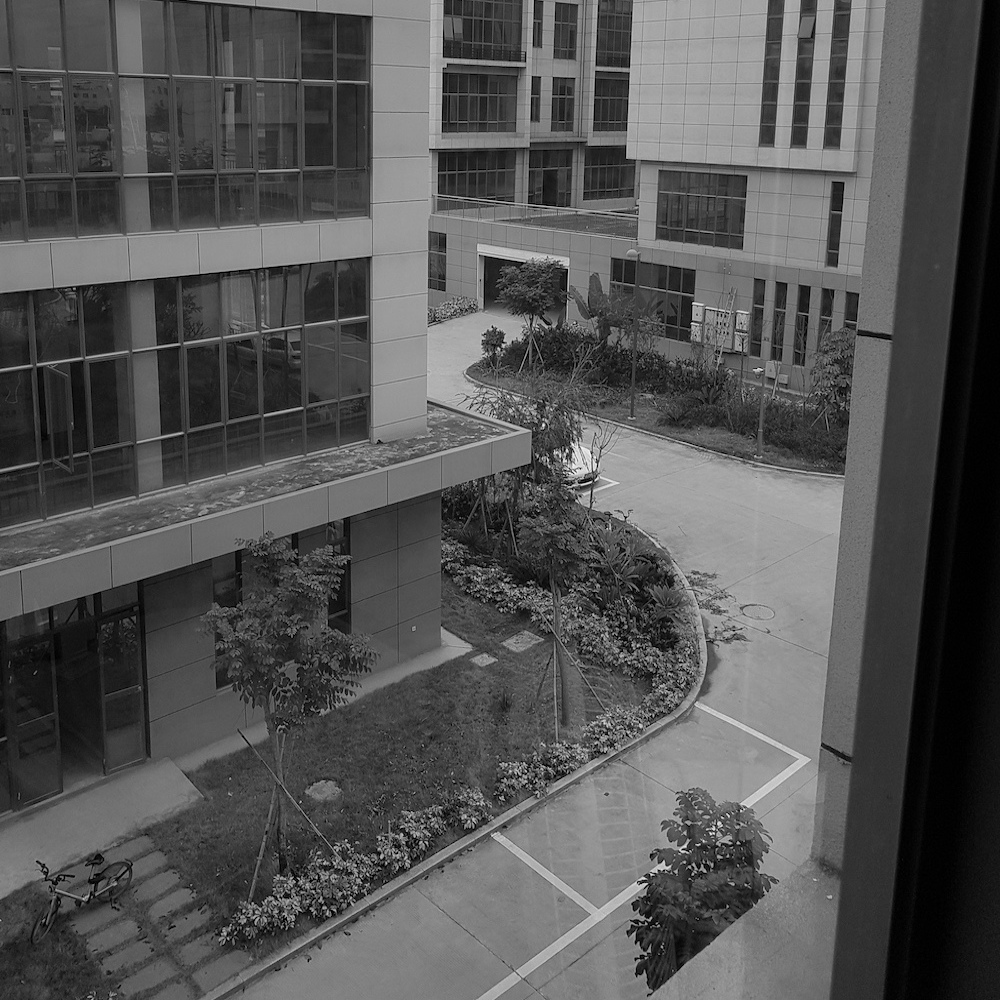
Our Best Investment
We feel very fortunate that we entered the carbon wheel business when we did, as we were at the forefront when the industry really started to change. Ten years ago we would have steered clear of carbon manufacturing in China. Today, we frequently travel to the factory for weeks at a time to focus on product development sessions, but make sure we leave enough time for a cultural connection. We are confident in our edge over our competition as we have such heavy influence on how our products are made. Every year we collaborate and participate in various exhibitions, cycling events, and factory visits to advance our knowledge. Partnering with a forward thinking Chinese company investing in the cycling industry is the best relationship we’ve built.
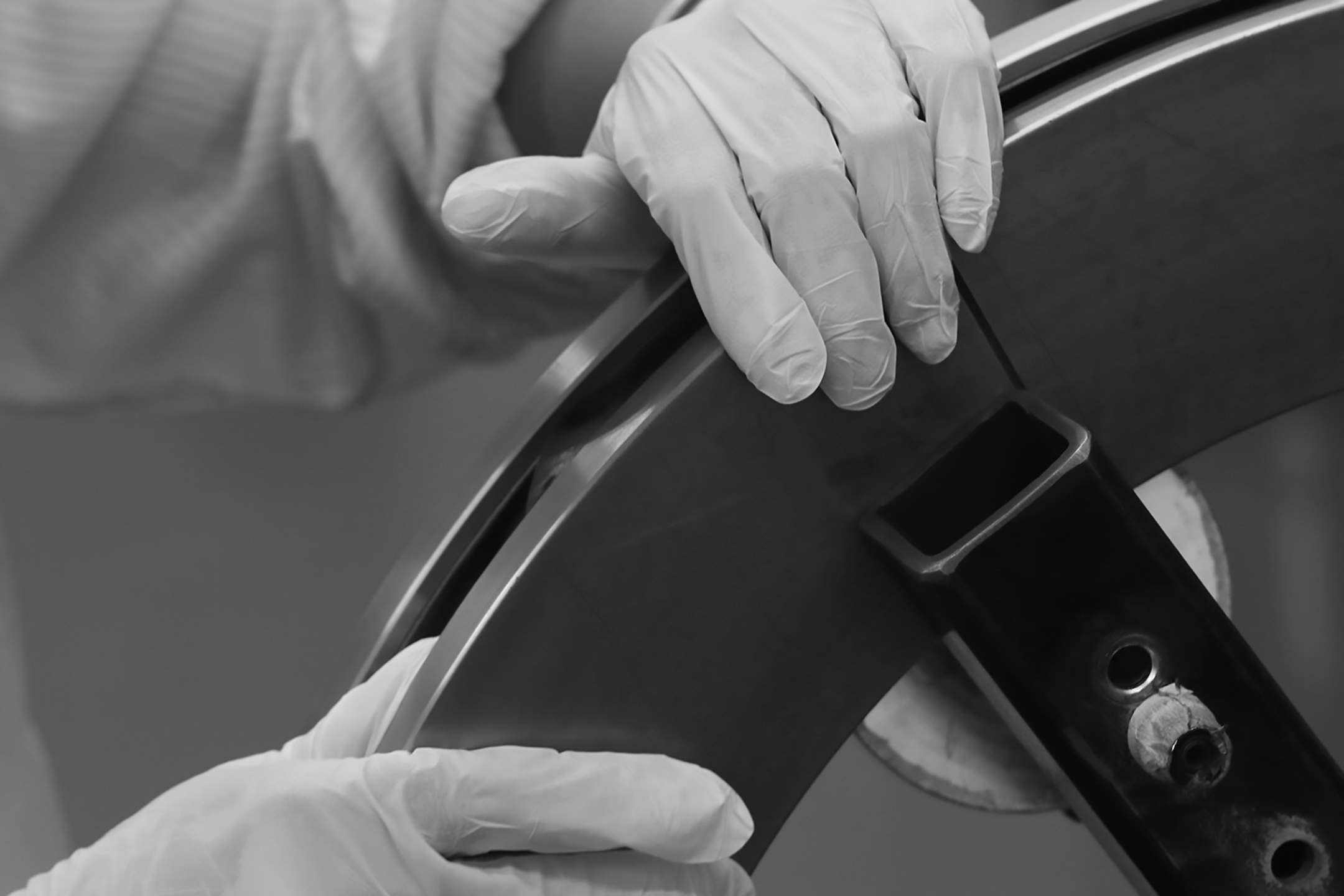
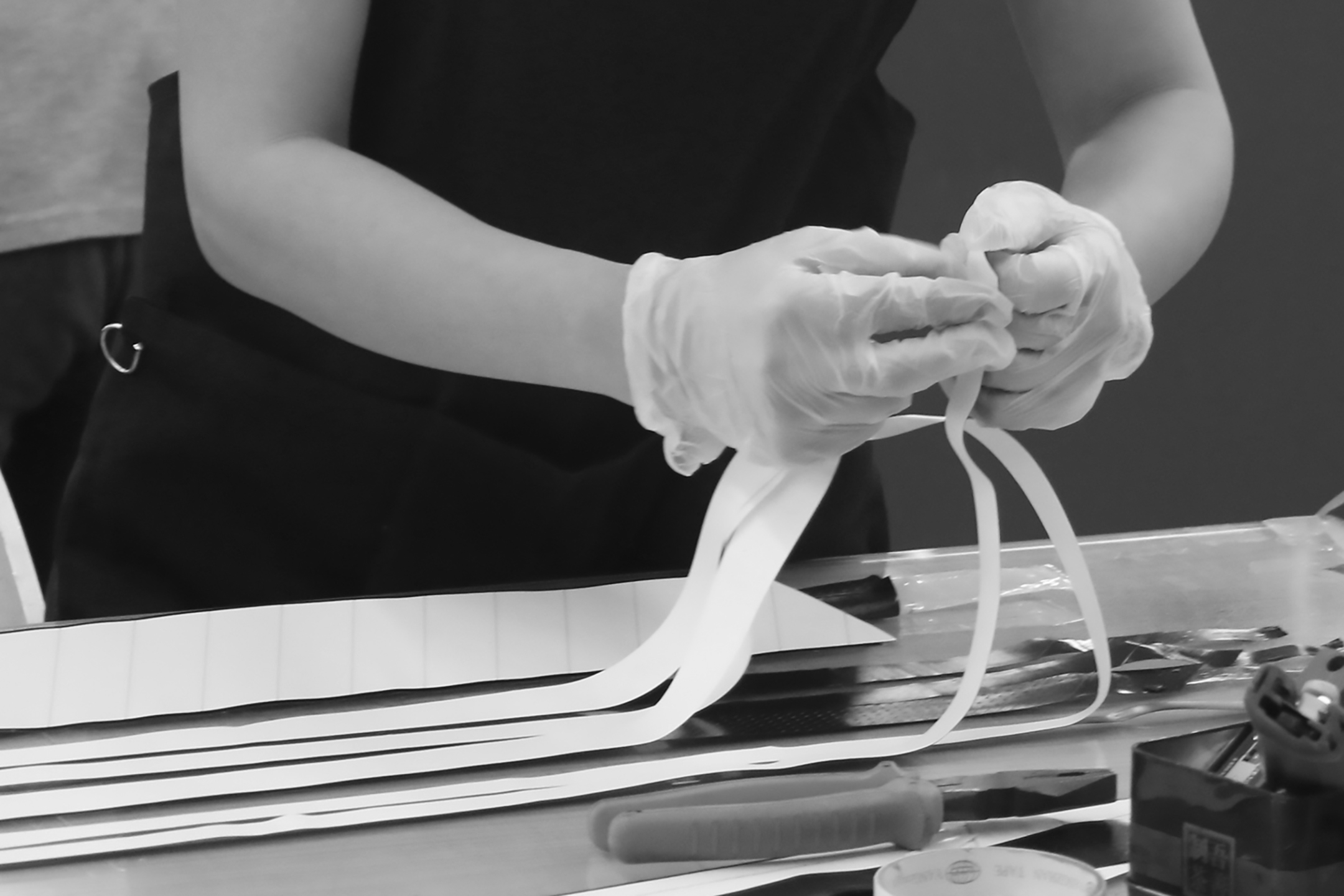